
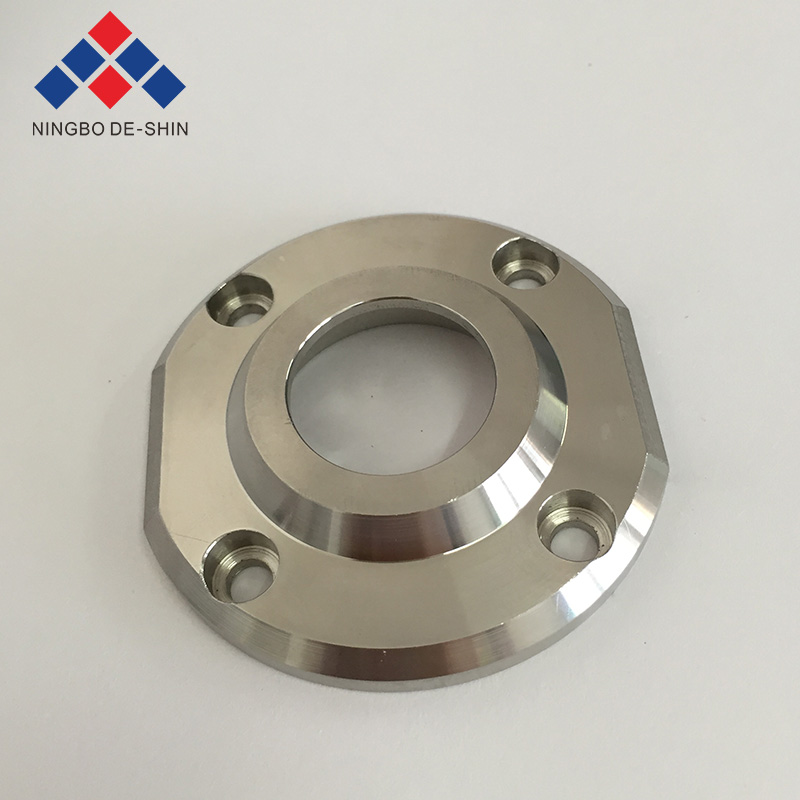
- #FEATURE CAM FOR SODICK WEDM FULL#
- #FEATURE CAM FOR SODICK WEDM SOFTWARE#
- #FEATURE CAM FOR SODICK WEDM SERIES#
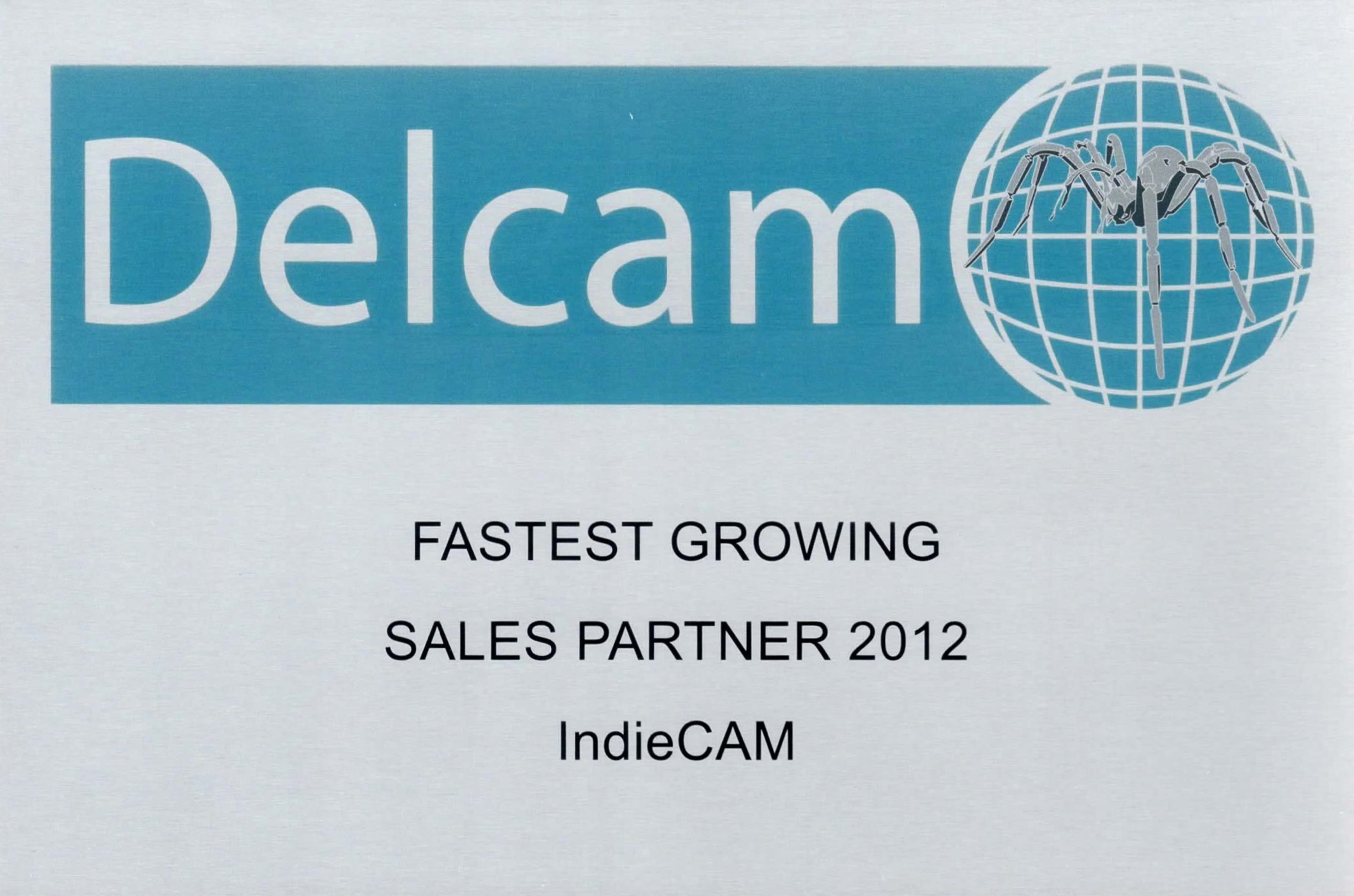
This is why we offer a 10-Year Positioning Accuracy Guarantee on our linear motor driven Wire and Sinker EDMs. The automatic wire threading unit 'FJ-AWT' with a high wire threading rate supports automatic operation. Since its release in 1981, Sodick's oil machining wire-cut EDMs have played a successful role in numerous sites. This dedication encompasses, not only the sale of our machines, but includes training, technical support and providing vital consumable products to ensure your machine runs at a optimal level.Īt Sodick, we believe in our product. The 'High-speed Eco-Cut O-Plus' reduces machining time and the number of cuts at Rz 1 um or less. Sodick’s mission statement is “Create, Implement and Overcome Difficulties.” This statement contains the company’s strong philosophy of “contributing to our customers’ manufacturing by creating new things, implementing them, and overcoming the difficulties involved in the process.”Īs the industry leader, we are committed to the highest quality standards. Our commitment to the highest quality standards does not stop at sales but applies equally to providing advice and support for applications, training, parts and service. Sodick EDMs enable the user to become the envy of their competition. Our machines are used for the production of dies, molds and other various applications which cannot be produced by standard machining methods. Although this compensation feature is most valuable in extreme taper cutting operations, it can be applied to any wire tool path involving independent U- or V-axis motions for improved accuracy.Since 1976, Sodick has manufactured over 60,000 EDM machines and over 45,000 Linear Motor Driven EDMs. The cutting results are measured and the resulting data is plugged into a formula that then provides the TPCMP value for each cutting pass. The appropriate compensation values are based on a simple test cut that the customer must do using his or her material and cutting parameters. An NC control system based on modern operating system used in conjunction with the power supply delivers outstanding results. The Sodick A530D Wire EDM machine at work burning a 1/2 wide key slot in a 10' tall 4' diameter steel tube.
#FEATURE CAM FOR SODICK WEDM SERIES#
According to developers, taper cutting accuracy improves from 0.00122 inch to 0.0008 inch. Sodick’s New Efficient Power Supply Unit The AG wire EDM series profits from Sodick’s latest generation of power supply unit, which is capable of high-speed, high precision and high-efficiency machining. The result is enhanced cutting accuracy and lower risk of wire breakage. This adjustment moves the wire slightly farther away from the surface at one end of the cut and slightly closer to the surface at the opposite end.
#FEATURE CAM FOR SODICK WEDM FULL#
Essentially, this change in wire angle adjusts the position of the wire in relation to the workpiece surface so that cutting conditions are the same along the full length of the wire in the cut. It enables the programmer to apply a single numerical value that determines the appropriate change in wire angle at both the upper and lower positions of the wire guides.

(Sudbury, Massachusetts).Ĭalled Volumetric Taper Compensation with four-axis overburn control or TPCMP (for toolpath compensation), this feature is available first on the FANUC RoboCut a-CiA series of wire machines equipped with FANUC series 31i-WB controls.
#FEATURE CAM FOR SODICK WEDM SOFTWARE#
Training on this software as a tool for DXF importation into the machine to create the tool path (NC program) is provided. HeartNC programming is used for the examples cut in class. The Machine Operation course is recommended for all new users to Sodick EDM equipment. A feature to compensate for this effect has been introduced on FANUC wire EDM models from Methods Machine Tools Inc. Wire EDM Class The Wire EDM Class is 3 days long. In addition to degrading geometric accuracy, this concentration of sparks may also cause the wire to break. The slower relative speed causes the energized wire to remove proportionately more material by producing an unwanted concentration of spark action in this portion of the workpiece. This change in relative wire traverse speed creates conditions for an overburn where the part shape is tighter or narrower. One of the chief difficulties in these situations arises because the wire traverse speed relative to the workpiece surface becomes slower as the wire approaches the progressively tighter arc of the cone shape or the narrower width of the slope.

Another example is cutting a slope in which the angle of the slope varies because one end of the slope is wider than the other. One example is a taper cut that follows a curve such as to produce a cone-shaped geometry. Cutting tall, steeply tapered surfaces with wire EDM is a challenging operation, especially if the wire must travel a greater distance at opposite ends of the taper in four-axis moves.
